강체전차선로 국산화로 전기철도 기술 향상 이끌다
올해 우리회사는 Biz. 모델 혁신 가속화를 위해 모듈연구소를 신설했다. 모듈연구소를 이끄는 배상준 수석연구원은 올 3월 광역철도와 고속철도에 쓰이는 강체전차선로 부품 국산화에 기여한 공로를 인정받아 ‘대한민국 엔지니어상’을 수상하기도 했다. 강체전차선 시스템 개발 과정의 숨은 이야기를 들어보자.
모듈연구소 배상준 수석연구원, 장광동 책임연구원
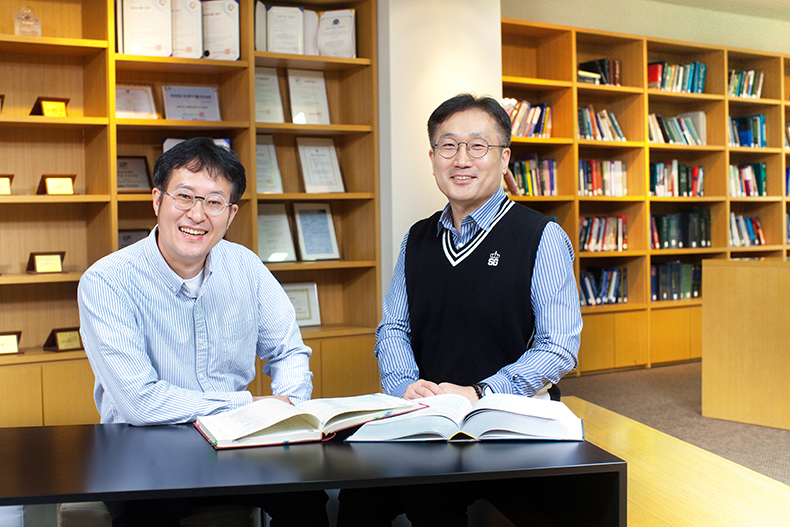
단순 제품 공급 넘어 엔지니어링 시스템까지
철도차량에 전기를 공급하는 전차선에도 여러 종류가 있다. 그중 기술적 장벽이 높아 오랫동안 유럽 제조사가 독점해왔던 강체전차선로를 우리회사가 국내 최초로 국산화에 성공했다. 배상준 수석연구원은 과제의 책임자로 전체 개발 과정을 진두지휘했고, 장광동 책임연구원은 설계, 시제작, 기능시험 및 현장모의시험 등의 전 과정에 참여했다. 우리회사가 성공한 이후 국산화에 나선 기업이 여럿 있었지만, 모두 중도에 포기했을 만큼 쉽지 않은 과정이었다.
“강체전차선로 방식은 T-BAR와 R-BAR로 구분되는데, 우리회사가 국산화에 성공한 것은 R-BAR 방식입니다. 강체전차선은 연결금구, 이행장치, 브래킷, 지지클램프, 신축이음장치, 램프 등의 구성품을 사용하는데, 단순 철도 부품 공급이 아닌 전체 엔지니어링이 수반되어야 하는 시스템입니다. 안정성을 중시하기 때문에 현장 설치 검증도 반드시 필요하고요. 기술적 요구가 높은 분야라 국산화가 쉽지 않은 상황이었습니다.”
장광동 책임의 설명처럼 강체전차선 시스템은 그동안 유럽산 제품과 기술에 의존해왔다. 그러나 최근 유럽과 일본 등 이른바 철도 선진국과의 기술 격차가 줄어들면서 자연스럽게 개발이 이루어졌다.
배상준 수석은 프로젝트가 시작된 지난 2010년 당시를 떠올렸다.
“시장 확대를 위해 단품이 아닌 고부가이면서 동시에 시스템 단위 공급이 가능한 철도 제품을 검토했습니다. 강체전차선의 R-BAR 방식은 우리회사의 알루미늄 압출 기술과 합금 기술을 활용하는 제품이라 충분히 개발이 가능할 것으로 보였습니다. 이후 강체전차선로에 필요한 모든 부품으로 개발 범위를 확대했고 현장 설치까지 이어졌습니다.”
현재 우리회사가 개발한 강체전차선로는 중저속용과 고속용으로 구분된다. 중저속용은 기존에 유럽에서 수입한 제품과 호환이 가능하도록 개발했고 고속용은 독자적인 구조로 개발을 진행했다.
“중저속용 제품은 2011년 본격적으로 개발에 착수해 2013년 현장 설치 검증까지 완료함으로써 초기 사업화에 성공했습니다. 수인선 연장선, 성남-여주선, 소사-원시선, 현재 공사 중인 소사-대곡 등 여러 구간에 설치됐습니다.”
고속용 제품은 2014년부터 2018년까지 국책과제로 개발이 진행됐다. 구조 설계, 부품별 평가, 테스트베드에서의 시공성 평가, 차량운행 시험 등을 거쳐 철도시설성능 검증서를 발급받았고, GTX-C 구간에 제품을 제안 중이다.
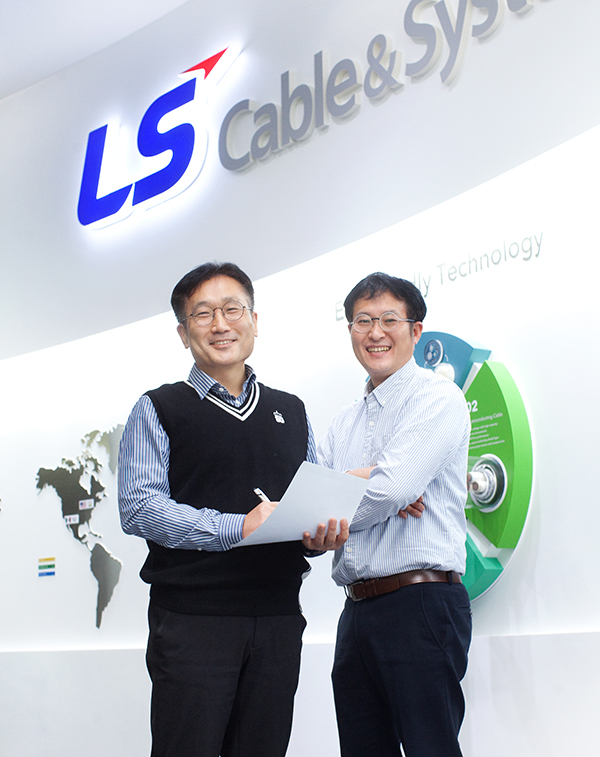
전선 분야 외 새로운 사업 기회 모색
강체전차선로 국산화 개발 뒤에는 수많은 노력이 숨겨져 있다. 오랜 기간 직접 현장에 나가 수많은 설치 시험을 진행했기 때문에 꺼내놓는 에피소드도 다양하다. 장광동 책임은 가장 힘들었던 순간으로 한여름에 진행된 운행 시험을 꼽았다.
“기존 해외 제품을 철거하고 우리 제품을 설치해 직접 차량을 운행해보는 시험을 했습니다. 철도공사에 허가를 받고 일정 시간 동안 전기를 단전시킨 후, 빠르게 철거와 설치를 모두 완료해야 하는 상황이었어요. 시간이 촉박해서 두 차례의 추가 단전을 요청하고 마지막에 아슬아슬하게 마무리했죠. 실제 차량이 운행됐을 때 사고가 나지는 않을지 마음 졸이며 지켜봤던 기억이 납니다.”
배상준 수석은 당시 아찔했던 순간도 함께 떠올렸다.
“철거 자재를 인근 변전소 부지로 운반할 때 비가 많이 내렸어요. 장광동 책임과 쫄딱 젖으며 자재를 적재했죠. 당시 폭풍우가 심해 철거 자재를 장막으로 덮어놨었는데, 그 장막이 바람에 날려 인근 철책에 걸려 있는 모습을 본 순간 정말 등에서 식은땀이 흐르더군요. 철거 자재가 전차선로로 날아갔다면 대형 사고가 났을 뻔한 아찔한 상황이었어요.” 강체전차선로 개발은 기존 수입 제품의 모방이 아닌, 분석과 개량을 통해 우리회사만의 차별화된 시스템을 개발했다는 데 의미가 있다. 아울러 국내 최초 국산화로 빠른 납기와 기술 대응 등이 가능해져 국가 철도 기술 발전에도 이바지했다.
우리회사는 이번 성공을 발판으로 더욱 다양한 진단 및 모니터링 모듈 발굴과 개발에 힘을 쏟을 예정이다. “강체전차선로와 같은 새로운 분야의 제품을 발굴하고 사업화해 우리회사의 사업 모델을 바꾸는 데 기여하고 싶습니다. 매출 규모 100억 단위의 모듈/시스템 제품을 10개 정도 사업화하는 것이 목표입니다. 모듈 제품도 하나의 사업단위가 될 수 있도록 노력하겠습니다.”
이들의 거침없는 활약과 함께 모듈연구소가 새롭게 만들어나갈 앞으로의 행보를 기대해본다.
강체전차선로 국산화로 전기철도 기술 향상 이끌다
올해 우리회사는 Biz. 모델 혁신 가속화를 위해 모듈연구소를 신설했다. 모듈연구소를 이끄는 배상준 수석연구원은 올 3월 광역철도와 고속철도에 쓰이는 강체전차선로 부품 국산화에 기여한 공로를 인정받아 ‘대한민국 엔지니어상’을 수상하기도 했다. 강체전차선 시스템 개발 과정의 숨은 이야기를 들어보자.
모듈연구소 배상준 수석연구원, 장광동 책임연구원
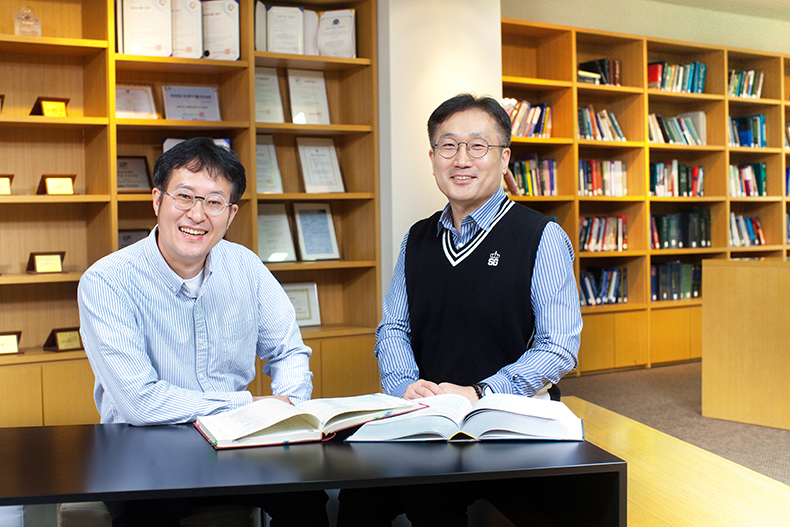
단순 제품 공급 넘어 엔지니어링 시스템까지
철도차량에 전기를 공급하는 전차선에도 여러 종류가 있다. 그중 기술적 장벽이 높아 오랫동안 유럽 제조사가 독점해왔던 강체전차선로를 우리회사가 국내 최초로 국산화에 성공했다. 배상준 수석연구원은 과제의 책임자로 전체 개발 과정을 진두지휘했고, 장광동 책임연구원은 설계, 시제작, 기능시험 및 현장모의시험 등의 전 과정에 참여했다. 우리회사가 성공한 이후 국산화에 나선 기업이 여럿 있었지만, 모두 중도에 포기했을 만큼 쉽지 않은 과정이었다.
“강체전차선로 방식은 T-BAR와 R-BAR로 구분되는데, 우리회사가 국산화에 성공한 것은 R-BAR 방식입니다. 강체전차선은 연결금구, 이행장치, 브래킷, 지지클램프, 신축이음장치, 램프 등의 구성품을 사용하는데, 단순 철도 부품 공급이 아닌 전체 엔지니어링이 수반되어야 하는 시스템입니다. 안정성을 중시하기 때문에 현장 설치 검증도 반드시 필요하고요. 기술적 요구가 높은 분야라 국산화가 쉽지 않은 상황이었습니다.”
장광동 책임의 설명처럼 강체전차선 시스템은 그동안 유럽산 제품과 기술에 의존해왔다. 그러나 최근 유럽과 일본 등 이른바 철도 선진국과의 기술 격차가 줄어들면서 자연스럽게 개발이 이루어졌다.
배상준 수석은 프로젝트가 시작된 지난 2010년 당시를 떠올렸다.
“시장 확대를 위해 단품이 아닌 고부가이면서 동시에 시스템 단위 공급이 가능한 철도 제품을 검토했습니다. 강체전차선의 R-BAR 방식은 우리회사의 알루미늄 압출 기술과 합금 기술을 활용하는 제품이라 충분히 개발이 가능할 것으로 보였습니다. 이후 강체전차선로에 필요한 모든 부품으로 개발 범위를 확대했고 현장 설치까지 이어졌습니다.”
현재 우리회사가 개발한 강체전차선로는 중저속용과 고속용으로 구분된다. 중저속용은 기존에 유럽에서 수입한 제품과 호환이 가능하도록 개발했고 고속용은 독자적인 구조로 개발을 진행했다.
“중저속용 제품은 2011년 본격적으로 개발에 착수해 2013년 현장 설치 검증까지 완료함으로써 초기 사업화에 성공했습니다. 수인선 연장선, 성남-여주선, 소사-원시선, 현재 공사 중인 소사-대곡 등 여러 구간에 설치됐습니다.”
고속용 제품은 2014년부터 2018년까지 국책과제로 개발이 진행됐다. 구조 설계, 부품별 평가, 테스트베드에서의 시공성 평가, 차량운행 시험 등을 거쳐 철도시설성능 검증서를 발급받았고, GTX-C 구간에 제품을 제안 중이다.
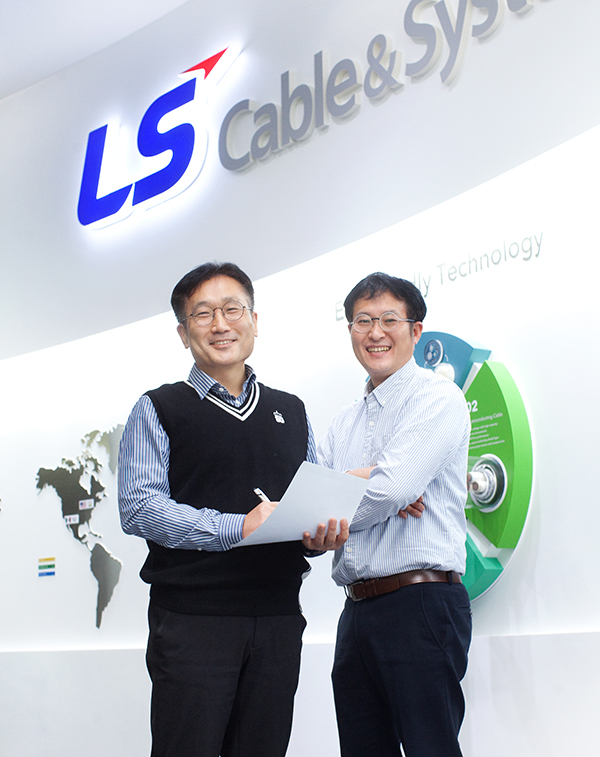
전선 분야 외 새로운 사업 기회 모색
강체전차선로 국산화 개발 뒤에는 수많은 노력이 숨겨져 있다. 오랜 기간 직접 현장에 나가 수많은 설치 시험을 진행했기 때문에 꺼내놓는 에피소드도 다양하다. 장광동 책임은 가장 힘들었던 순간으로 한여름에 진행된 운행 시험을 꼽았다.
“기존 해외 제품을 철거하고 우리 제품을 설치해 직접 차량을 운행해보는 시험을 했습니다. 철도공사에 허가를 받고 일정 시간 동안 전기를 단전시킨 후, 빠르게 철거와 설치를 모두 완료해야 하는 상황이었어요. 시간이 촉박해서 두 차례의 추가 단전을 요청하고 마지막에 아슬아슬하게 마무리했죠. 실제 차량이 운행됐을 때 사고가 나지는 않을지 마음 졸이며 지켜봤던 기억이 납니다.”
배상준 수석은 당시 아찔했던 순간도 함께 떠올렸다.
“철거 자재를 인근 변전소 부지로 운반할 때 비가 많이 내렸어요. 장광동 책임과 쫄딱 젖으며 자재를 적재했죠. 당시 폭풍우가 심해 철거 자재를 장막으로 덮어놨었는데, 그 장막이 바람에 날려 인근 철책에 걸려 있는 모습을 본 순간 정말 등에서 식은땀이 흐르더군요. 철거 자재가 전차선로로 날아갔다면 대형 사고가 났을 뻔한 아찔한 상황이었어요.” 강체전차선로 개발은 기존 수입 제품의 모방이 아닌, 분석과 개량을 통해 우리회사만의 차별화된 시스템을 개발했다는 데 의미가 있다. 아울러 국내 최초 국산화로 빠른 납기와 기술 대응 등이 가능해져 국가 철도 기술 발전에도 이바지했다.
우리회사는 이번 성공을 발판으로 더욱 다양한 진단 및 모니터링 모듈 발굴과 개발에 힘을 쏟을 예정이다. “강체전차선로와 같은 새로운 분야의 제품을 발굴하고 사업화해 우리회사의 사업 모델을 바꾸는 데 기여하고 싶습니다. 매출 규모 100억 단위의 모듈/시스템 제품을 10개 정도 사업화하는 것이 목표입니다. 모듈 제품도 하나의 사업단위가 될 수 있도록 노력하겠습니다.”
이들의 거침없는 활약과 함께 모듈연구소가 새롭게 만들어나갈 앞으로의 행보를 기대해본다.